Charlie Norwood Medical Center
Raymond was engaged at the Charlie Norwood VAMC to address on-going water infiltration issues. The facility was experiencing water migration throughout the building enclosure and retaining walls which was resulting in leaks, stained concrete, and peeled finishes. Additionally, the building enclosure needed cleaning and general maintenance, and rain water was causing corrosion at exterior handrails. The main source of water entry at the precast concrete wall panel cladding was deteriorated sealant at control joints and open wall expansion joints.
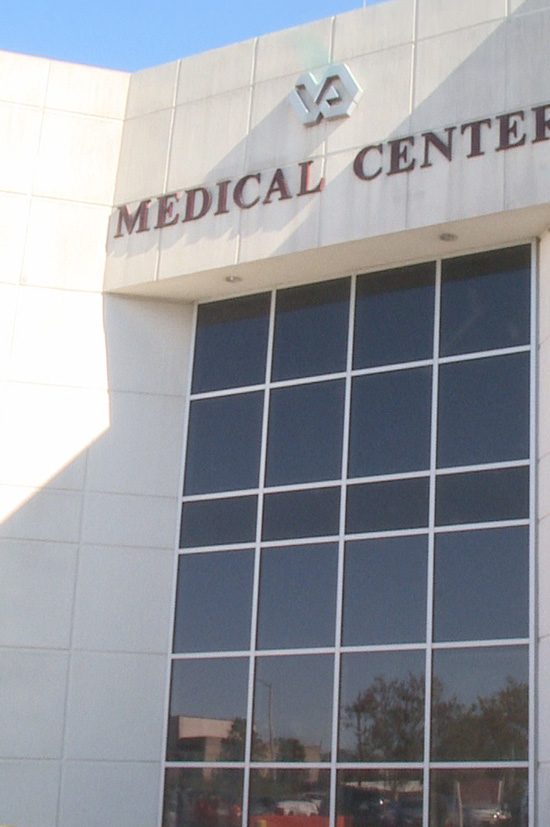
Client: U.S. Department of Veterans Affairs
Location: Augusta, GA
Size: 2,490 SF
Estimated Construction Cost: $2,500,000
Services Provided:
- Project Management
- Field Verification
- Building Envelope Design
- Civil / Structural
- Construction Administration
Benefits/Challenges
Unique Challenges
The pedestrian roof plazas over lower floors experienced leaks from an unknown source and the expansion joints were not visible or readily accessible. This required the team to perform a careful review of the building’s plans, so as to minimize the requisite intrusive testing to determine exact locations.
Initial surveys confirmed that expansion joints at the plazas were improperly constructed with no relief for natural expansion and contraction of the building. Raymond identified a manufacturer whose membrane expansion joint were compatible with the modified bitumen roofing, and then developed details to install an accessible expansion joint cover to meet the manufacturer’s warranty requirements.
Our Value Add
Due to the phased contracting approach, the initial contract award, design work, and construction phase spanned several years. This led to the Raymond team working with three separate VA Project Managers (PM). In each case, our Raymond Program Manager was able to meet with the new PM and review all documentation to bring the PM up to speed rapidly.
Due to the nature of the water intrusions, the original contract solicitation did not provide significant detail on the required work to be completed. Raymond spent additional time at the project site to ensure survey findings were understood by the owner, and the correct direction and requirements were outlined prior to additional work being initiated.
Raymond’s initial cost estimating proved useful when the VA released its contractor solicitation. While the VA preferred contracting with a small business or disadvantaged firm, this would have increased costs by 50% over the initial estimates (due to regional small businesses not possessing the ability to self-perform the required type of work). Raymond was able to identify the issues and worked with the VA to re-scope the solicitation to provide the government with the best option for the requisite services, while optimizing for cost (estimated $1.3 M in savings).
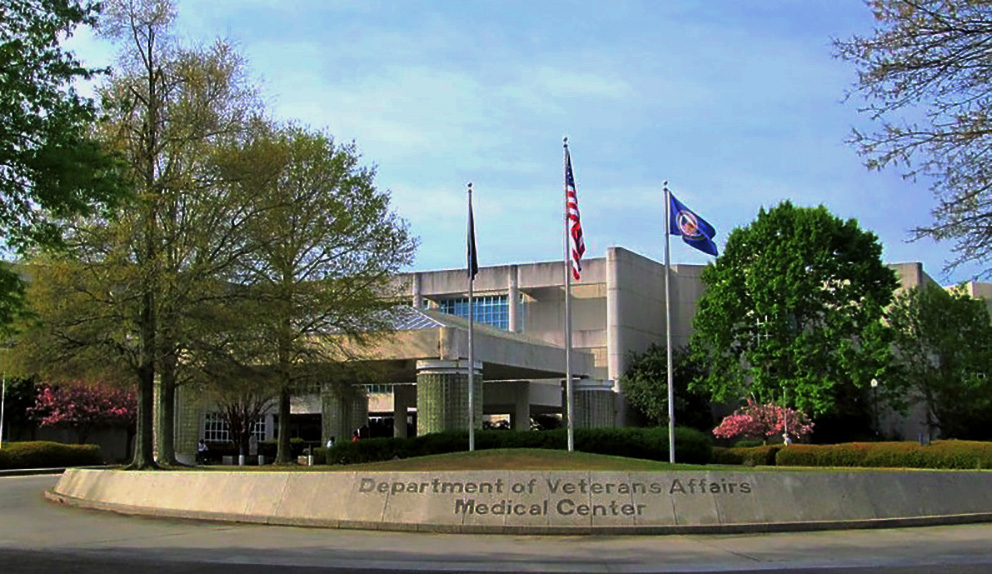